HyPatchRepair 项目证明了用于焊接热塑性复合材料补片修复的自动化工艺链的可行性。
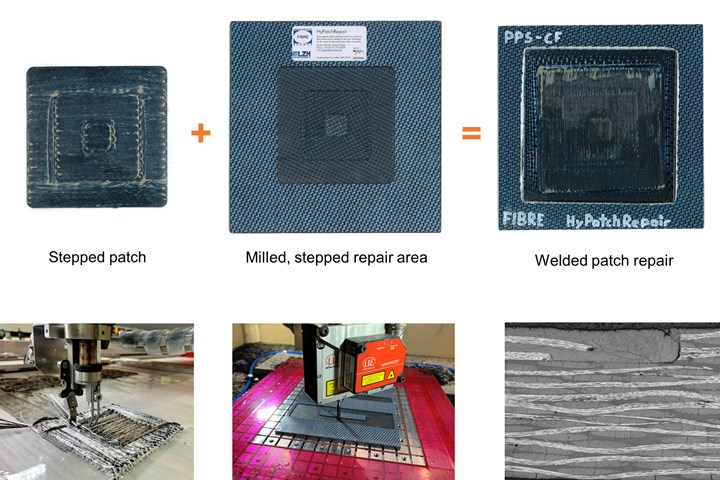
演示焊接热塑性复合材料 (TPC) 补片修复
HyPatchRepair 项目(从左到右,上图和下图)将使用定制纤维铺放 (TFP) 制成的阶梯式修复补片与具有相同结构的铣削面板配对,并使用压焊将它们集成在一起展示自动化 TPC 修复过程链的可行性(参见显微照片顶部的焊接补丁)。图片来源:HyPatchRepair 项目,Faserinstitut Bremen
图像在顶部,与标题一致:DMG Mori Ultrasonic MobileBLOCK 机器人将修复区域铣削成台阶,之后集成的 Wenglor 激光轮廓扫描仪将测量表面的精度。图片来源:HyPatchRepair 项目,Faserinstitut Bremen
热塑性复合材料 (TPC)继续在越来越大的飞机结构中得到展示,提供快速制造以满足未来窄体和先进空中机动 (AAM) 平台预期的更高生产率。TPC 结构还支持焊接组件,无需紧固件,从而进一步减少生产时间、成本和重量。在最近的博客中,一级飞机结构供应商Spirit AeroSystems(美国堪萨斯州威奇托)解释说,“在较大的部件中使用热塑性塑料,如纵梁、框架、舱壁和机身蒙皮面板,可能非常有益。我们的目标是在可以实现自动化高速制造的应用中使用热塑性复合材料……在非常短的循环时间内反复熔化、成型和固化材料。”
但是,使用中的飞机会损坏,而损坏需要修理。热固性复合材料的修复技术得到了很好的发展,包括使用粘合复合材料修复补丁修复初级结构的常用方法(参见“再看复合材料结构的粘合锥形围巾修复”)。尽管 TPC 结构自 1990 年代以来就已投入使用,但类似的修复技术仍在开发中。
HyPatchRepair项目(2019-2022) 由德国政府资助,作为 LuFo-V3 航空航天研究计划的一部分,旨在展示连续纤维增强 TPC 零件的无铆钉修复技术。目标是一套自动化修复技术,以在不增加机身蒙皮、机翼、小翼和尾翼部件(包括方向舵)等部件重量的情况下恢复原始承载能力、几何形状和空气动力学表面。这些技术将准备修复区域,制作负载优化的修复补丁,然后使用经过验证且具有成本效益的技术将补丁集成到修复区域。
自动化修复流程链
德国 HyPatchRepair 联盟由研究机构 Faserinstitut Bremen(FIBRE,隶属于不来梅大学)和 Laser Zentrum Hannover(LZH,汉诺威)牵头。该项目包括空中客车运营部、飞机维修服务提供商 Lufthansa Technik(汉堡)、小型飞机制造商 Silence Aircraft (Schloß Holte Stukenbrock) 和光学测量系统供应商 Vereinigte Elektronikwerkstätten(VEW,不来梅)作为相关合作伙伴。由于其在大型 TPC 结构方面的专业知识,GKN Fokker (Hoogeveen,荷兰)提供了缺陷/损坏案例并帮助定义了演示器。
该联盟构想的工艺链包括:
- 检测损坏:光学测量系统检查要修复的零件并确定需要去除的材料的面积和深度,并尽可能减少这种情况。VEW 在其设施中使用光学测量系统演示了这一步骤。
- 铣削修复区域:使用DMG MORI (德国比勒费尔德)五轴 ULTRASONIC mobileBLOCK 机器人去除损坏的材料,提供一致的质量、尺寸精度和可重复性。为了用精确的修复补丁替换移除的层,修复区域被加工成台阶。FIBER 使用 DMG MORI 机器人演示了这一过程,而 LZH 使用激光进行了探索。
- 测量修复区域:必须准确测量阶梯式修复区域,以制作精确贴合的修复补丁。LZH 使用 Wenglor(德国泰特南)MLWL 232 激光轮廓扫描仪演示了此步骤。LabVIEW 软件(National Instruments,Austin,Texas,US)用于将数据转换为所需的贴片尺寸。
- 制造修复补丁:修复补丁预制件使用定制纤维放置 (TFP) 和连续纤维 3D 打印制造,然后进行加固。FIBER 演示了使用热压机和专门设计的工具制造 TPC 预成型件和固结。
- 修剪补片:补片在加固后进行测量,并与阶梯式修复表面进行比较。LZH 演示了使用激光完成所需的修整。
- 焊接补片:使用激光束焊接将补片熔合到修复区域。LZH 展示了这种方法的工作原理,而 FIBER 展示了在热压机中使用压力焊接的概念。
请注意,HyPatchRepair 的目标是展示此工艺链的可行性并完成参数测试以了解和选择最佳工艺选项。研究的材料包括碳纤维 (CF) 增强聚酰胺 6 (PA6) 和聚苯硫醚 (PPS)。后续项目 ThermoRep3D (2022-2025) 将进一步开发这些工艺步骤,包括将弯曲贴片制造和焊接/熔合到弯曲修复区域,以及使用碳纤维增强低熔点聚芳醚酮 (LM-PAEK)胶带材料。
适用于 HyPatchRepair 的机器人方法
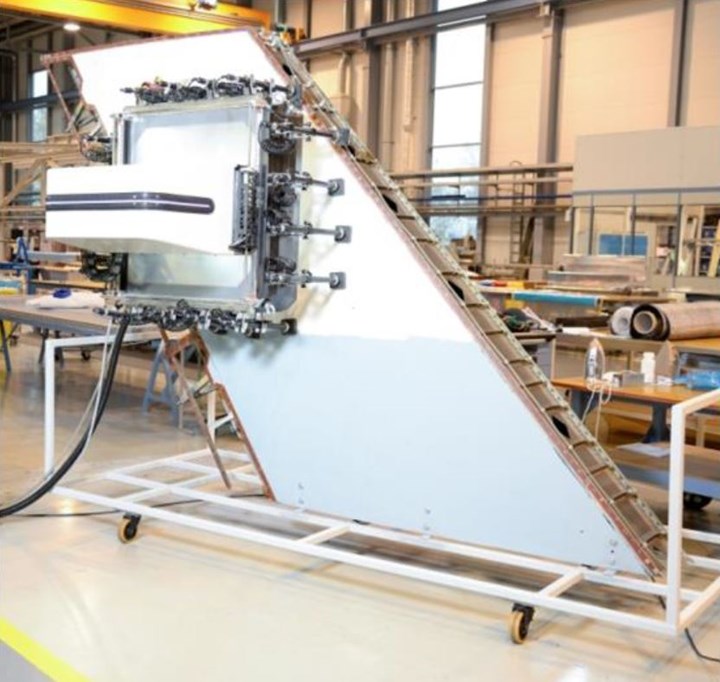
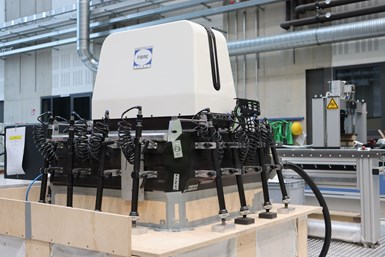
图 1. 改装的机器人单元
HyPatchRepair 中使用的 DMG MORI 机器人在 CTC 体育场的垂直鳍片(顶部)上进行了测试,经过修改后在 FIBER 的临时胶合板单元内的平板上进行铣削和扫描(底部)。 图片来源:HyPatchRepair 项目,Faserinstitut Bremen
10 年前,在由 Lufthansa Technik 和 Airbus 领导的复合材料适应性检查和修复 (CAIRE) 项目 (2012-1015) 中,探索了使用机器人进行粘合补丁修复的热固性复合材料。CAIRE 开发的机器人和上面的 DMG MORI 机器人在CW 2016 年的文章“ Aircraft composite repair moves toward maturity”中进行了讨论。” 美国 GFM(美国弗吉尼亚州切萨皮克)开发了一种类似的机器人方法(参见“迈向便携式、数字化复合零件修复”)。HyPatchRepair 的任务是如何针对 TPC 零件调整此过程。
FIBRE 的 HyPatchRepair 项目经理 Markus Geiger 指出,DMG MORI 机器人之前位于空中客车公司的复合材料技术中心(CTC,Stade,德国)。“我们把它带到了 FIBRE 的ECOMAT 中心,紧邻不来梅的空中客车运营中心,然后对其进行了修改。” 他解释说,该机器人设计用于连接到飞机机身上。但由于 HyPatchRepair 中的试验将在平板上进行,因此FIBER 创建了一种研发单元,机器人可以在其中执行扫描以及使用真空除尘进行铣削(图 1)。使用配备铣削工具和激光线扫描仪的单个末端执行器(步骤 1),可以进行这两项操作。
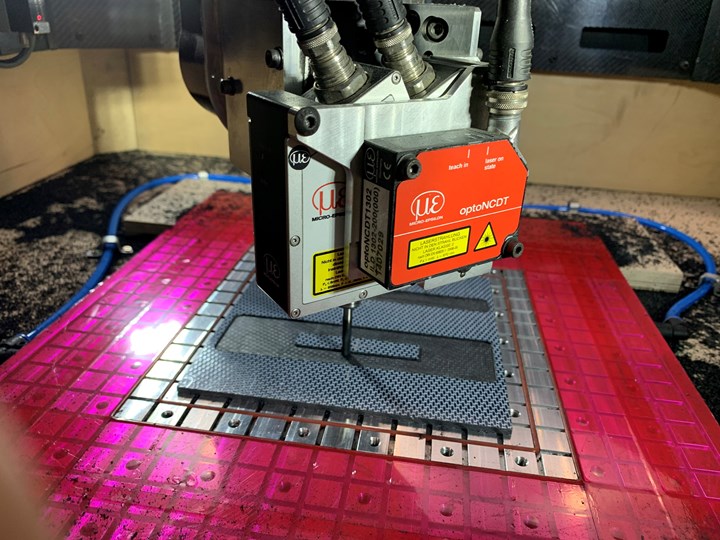
步骤 1.机器人踏入演示面板。也连接到末端执行器的激光轮廓扫描仪将扫描加工表面以确保准确性。图片来源:HyPatchRepair 项目,Faserinstitut Bremen
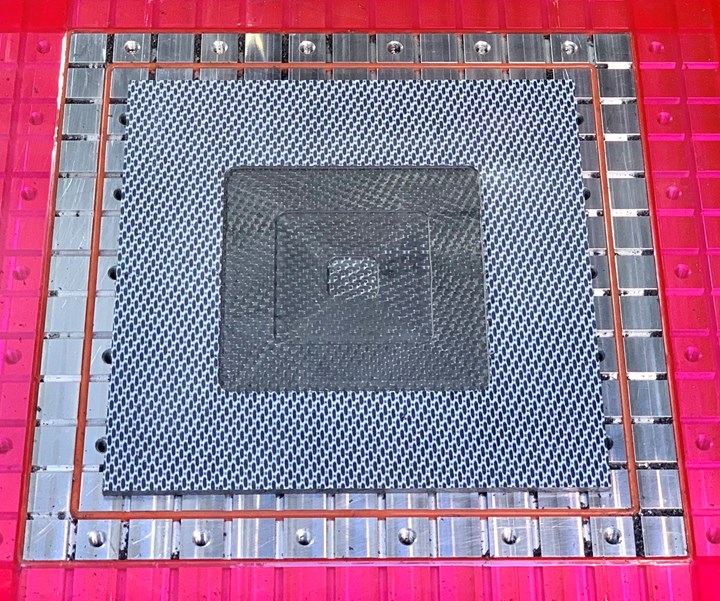
第 2 步。准备扫描修复区域中加工的三个 20 毫米宽的台阶。图片来源:HyPatchRepair 项目,Faserinstitut Bremen

第 3 步。 使用 CF/PPS 纤维的定制纤维铺放 (TFP) 产生 100、60 和 20 毫米宽的台阶作为单个 100 × 100 毫米的修复补丁。图片来源:HyPatchRepair 项目,Faserinstitut Bremen
铣削和补丁演示
为了演示 TPC 补丁修复,HyPatchRepair 选择了一个 100 × 100 毫米的方形补丁,具有三个 20 毫米宽的台阶。必须制造演示面板,然后进行铣削以匹配这些步骤。在实际维修中,目标是恢复层压板,以便替换所有移除的材料,匹配每层的纤维方向。因此,DMG MORI 机器人被编程为在演示面板中铣削一个三级区域(步骤 1)。旋转末端执行器,然后机器人扫描铣削区域以确保精度(步骤 2)。铣削和扫描时间总计 30 分钟。
下一步是制造修复补丁。由于 HyPatchRepair 专注于 TPC 修复,该项目偏离了过去基于预浸料的工艺,而是试用了 TFP(第 3 步)和 3D 打印。这两种工艺都可以生产具有定制几何形状和纤维方向的修复补丁。TFP 使用工业缝合机将混合的热塑性塑料和增强纤维固定到基质兼容薄膜上(参见“从自然中汲取设计灵感……第 2 部分”)。正如CW 2017 年自动化预成型专题的第 2 部分所述, FIBER 与 TFP 有着悠久的合作历史,包括生产负载优化的 TPC 预制件,然后将其快速压塑或热成型为零件。对于每次试验,演示面板和修复贴片均使用相同的材料和工艺制成。
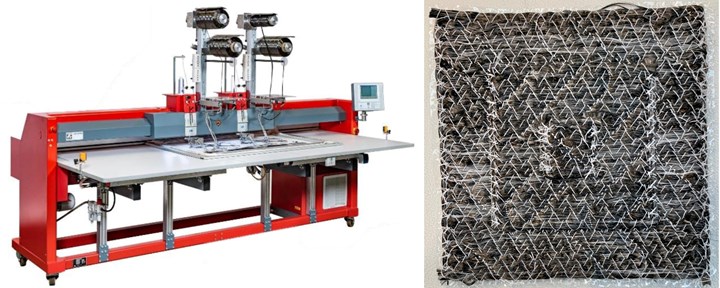
图 2. TPC 贴片的 TFP
ZSK 双头缝纫机(左)使用 12K 碳纤维/PPS 混合纱线和更高熔点的 PEEK 缝合线生产 TFP 贴片(右) 。图片来源:HyPatchRepair 项目,Faserinstitut Bremen
TFP 试验使用双针头ZSK Stickmaschinen(德国克雷费尔德 ZSK)机器和与 PA6 或 PPS 混合的 CF 纱线(图 2)。铺层堆叠顺序为 0°/90°/0°/90°/0°/90°。为了巩固(第 4 步),将每个贴片放入两件式钢制工具组中,并在热压机中热成型。CF/PPS 贴片的典型压制周期包括升温至 280°C(10 分钟),在 280°C 下停留 12 分钟,压力为 30 巴,然后冷却(10 分钟),同时保持该压力。固结后的层厚度约为 0.25 至 0.30 毫米。对于 CF/PA6 补片,升温 6 或 8 分钟至 240°C,然后在 240°C 下停留 10 分钟,然后冷却 8 至 15 分钟。压力从升温期间的 5 巴逐步增加到驻留期间的 10 巴,并在冷却期间增加到 20 巴。
3D 打印贴片是使用CTC Stade 的Markforged(美国马萨诸塞州沃特敦)Mark Two 机器和连续碳纤维长丝与尼龙 (PA) 长丝结合生产的。铺层堆叠顺序为每步 0°/90°/90°/0°。3D 打印后的层厚度约为 0.10 至 0.125 毫米。“我们曾希望使用连续纤维长丝,”Geiger 说,“但由于时间和其他因素,这是不可能的。打印出来的补丁仍然有很大的孔隙率,在与阶梯式修复区域融合之前需要加固。” 然而,在项目的这一点上,FIBER 已经决定专注于贴片制造的 TFP。
初审结果
Geiger 讨论了贴片制造过程中研究的各种参数和经验教训。例如,TFP 补丁使用了两种方法,他说,“一种是所有三个步骤都是一个补丁,另一种是我们对每个步骤使用单个补丁。在后者中,我们从较大的 TFP 样本中切割出 100、60 和 20 毫米宽的台阶。这避免了在 TFP 过程中在贴片边缘产生的纤维转弯 [请参见顶部打开图像中贴片边缘的环路]。” 这些车削往往会产生富含基质的区域,但他指出,从更大的面板上切下台阶会造成浪费。
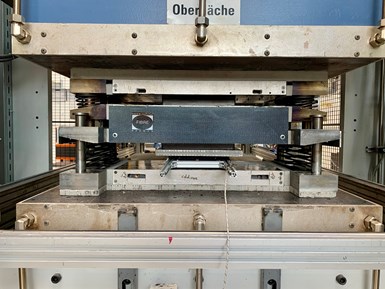
第 4 步。TFP 修复补丁在热压机中的两件式钢制工具中得到巩固。图片来源:HyPatchRepair 项目,Faserinstitut Bremen
另一个发现是在 CF/PA6 修复补丁的整合过程中发现的。“在这些补丁中,缝合纱线也是 PA6,”Geiger 说。“我们注意到在压力机合并过程中,缝线开始‘游动’,这意味着它产生的区域基质多于纤维。因此,我们随后针对 CF/PPS 样品调整了方法,并使用了熔点更高的聚醚醚酮 [PEEK] 缝合纱线。当我们整合这些补丁时,没有‘游泳’,我们获得了更好的质量。”
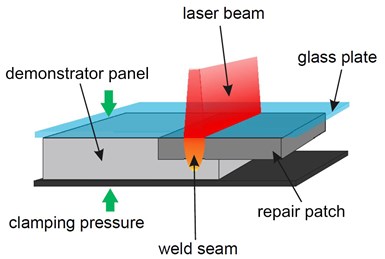
图 3. 基于激光的热传导焊接
二极管激光器穿过一块玻璃板 - 它在焊接夹具中的贴片上保持压力 - 并加热贴片中的 TPC 矩阵和配合的阶梯表面。当材料冷却时,会形成可靠的焊缝。图片来源:Laser Zentrum Hannover
激光焊接
HyPatchRepair 期间试用了两种焊接方法:基于激光的热 传导焊接和压焊,下面将对此进行讨论。激光焊接试验由 LZH 进行。“使用的一般方法,”LZH 复合材料负责人 Verena Wippo 解释说,“将修复补丁和要修复的演示面板放置到焊接夹具中,该焊接夹具使用玻璃板将修复补丁向下压到阶梯式修复区域 [步骤 6]。激光束穿过玻璃板产生热量,热量通过修复贴片传导。” 这种热量会熔化贴片中的基质,在阶梯式维修区的配合面。保持压力,随着激光通过,材料冷却,形成可靠的焊缝(图 3)。
LZH 使用Toray Advanced Composites(Nijverdal,荷兰)Cetex CF/PPS 有机片材进行了初步试验,底部有 10 层,包括 3 毫米厚的演示板,顶部有 4 层,用于 1.2 毫米厚的修复试片。中间需要一层额外的未增强 PPS 薄膜,以提供足够的基体材料,以确保部件之间的良好连接。这些材料使用 Laserline GmbH(Mülheim-Kärlich,德国)LDM 300-40 二极管激光系统加热,功率为 300 瓦,光斑几何形状为 11 × 40 毫米,波长为 940 纳米。
然后试验转移到 TFP 贴片和演示面板。然而,Geiger 指出,最初存在一些挑战。“例如,我们的贴片包括三个台阶,每个台阶深度为 0.6 毫米,总厚度为 1.8 毫米。但激光只能焊接 1.6 毫米的厚度。因此,LZH 不得不将焊接过程分为三个加热步骤,分别焊接三个补片层。”
这是通过实施一个使用高温计测量表面温度的控制系统解决的。“在几次测试中,LZH 测量了表面温度以及使用的激光功率和照射时间,”Geiger 说,“并将这些与对产生的焊缝的分析进行了比较。使用这些结果,LZH 能够根据高温计测量值调整焊接参数。最终实现了各台阶层的多级焊接和一次焊完整贴片的焊接。”
后者用于最终演示器,如下所述。LZH 在一次通过中同时照射整个修复补丁区域,由自动控制系统管理。该系统使用高温计测量的表面温度信号,它使用 PID(比例-积分-微分)控制器处理该信号,然后管理激光功率以保持指定的焊接温度。
另一个发展是用在演示面板中铣削修复步骤产生的废料代替 PPS 薄膜。“我们用这些废料制作了一个小箔片,将其作为第一层粘合层铺设在阶梯式修复区域,”Geiger 解释道。“这个层之后是补丁。这就是 LZH 所做的,因为他们需要更多的矩阵来使用激光工艺焊接贴片。这种重复使用的废料实际上比纯基质箔的性能更好,因为它含有少量碳纤维。”
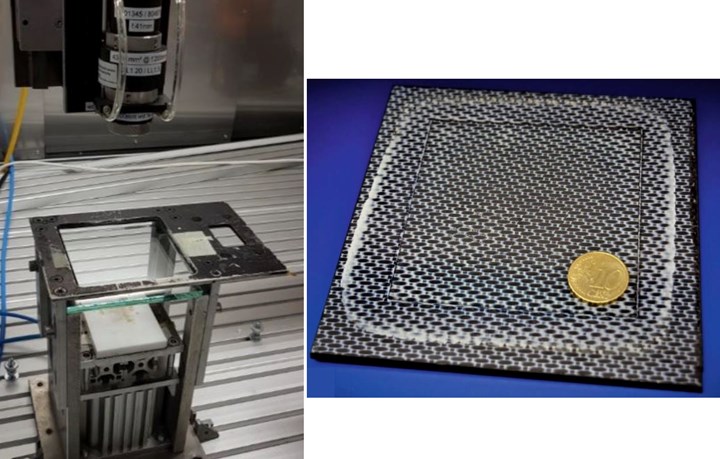
第 5 步。使用二极管激光系统和焊接夹具(左)将 TFP 修复贴片激光焊接到演示面板上。完成的修复显示总体质量良好,没有大的空隙,并且修复的每个步骤都连接到其匹配的基板(右)。 图片来源:HyPatchRepair 项目,Faserinstitut Bremen
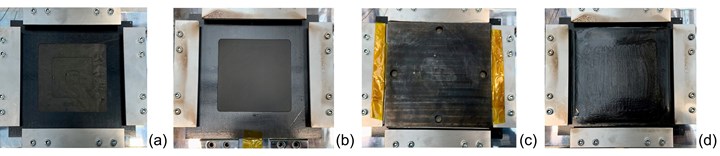
步骤 6.使用下方图 4 中的工具,将 TFP 修复贴片压焊到演示面板: (a) 压焊工具中的阶梯面板;(b) 与阶梯面板匹配的修复补丁;(c) 工具关闭;(d) 工具打开显示焊接修复面板。图片来源:HyPatchRepair 项目,Faserinstitut Bremen
压焊,最终演示
FIBER 选择压焊作为测试材料、工艺参数和在修复补片和阶梯修复区域之间实现良好焊接的要求的方法。这种方法是在最终演示面板的试验过程中开发的,用于生产30 多个压焊演示维修。
演示器中的修复补丁尺寸和几何形状与初始试验保持不变,而面板尺寸约为 160 × 160 毫米,以提供用于拉伸和三点弯曲测试的修复后试片。TFP 之所以被选为首选工艺,是因为该工艺简单、开发过程中的良好结果以及内部设备的可用性。使用的最终材料是Coats(英国布里斯托尔)Synergex 12K CF/PPS 混合纱线,部分缝合到 PPS 薄膜 Rayotec S 080 PPS 薄膜(Toray Advanced Composites)上,采用 PEEK 缝合纱线。

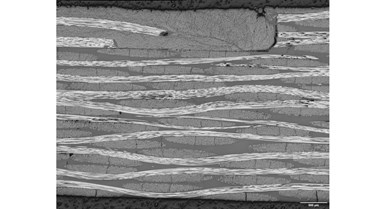
图 4. 压焊工具,结果
为了在压焊过程中将热量和压力限制在修复贴片上,使用了一个额外的分体压焊工具与贴片固结中的两件式工具结合使用(上图)。修复补片外缘的横截面显微照片显示了焊接的补片层(底部图像的左上角)。图片来源:HyPatchRepair 项目,Faserinstitut Bremen
根据修补补片加固期间的经验教训,FIBER 开发了 一种额外的钢制工具,可在压焊期间使用。与加固中使用的两件式工具一样,这种“分体式压制工具”也由两部分组成:底部包含绝缘环,顶部经过机加工以适合(图 4)。绝缘环仅将热隔离到修复补丁,而不是周围区域(图 4)。
位于两件式固结工具顶部下方并直接位于修复补丁的顶部,分离式压力工具充当一种压力增强器,与单独使用两件式工具相比,可最大限度地减少缺陷和孔隙。它还在贴片中保持足够的基质熔化,以形成与阶梯式面板的焊接连接。过程温度和压力遵循上面列出的用于固结的那些;处理时间总计 36 分钟(第 5 步)。
测试结果,前进的道路
完成了 6 个压焊修复和 4 个激光焊接修复的三点弯曲测试,结合强度分别为 572 至 655 兆帕和 594 至 645 兆帕——几乎是 800 兆帕时未损坏参考样本的 80%。
激光焊接演示器的拉伸测试表明,与一层相比,在贴片下方使用两层 PPS 层会增加失效载荷。随着拉伸载荷在 450 秒的最长焊接时间达到最大值 ≈17 千牛顿,这种增加会变窄。用于激光焊接修复的显微 CT(计算机断层扫描)分析显示没有富含空隙的区域,并确认所有贴片台阶都连接到它们的匹配基板(步骤 6)。
在后续项目中,ThermoRep3D、用于弯曲修复演示器的几何形状和材料已被定义,Geiger 说。“将修复单曲面和双曲面。除了 TFP 之外,我们还将研究使用胶带材料,并演示使用感应加热垫来执行贴片集成。” 最后一项技术的合作伙伴是msquare GmbH(德国斯图加特),该公司开发了电磁感应技术并获得了专利——通过电磁场通过电力产生热量——在可高达 400°C 的柔性加热毯中使用(参见“用于热塑性复合材料修复的柔性感应加热”)。
“我们已经证明,这个工艺链可以进行焊接修复,并且在我们对相关技术的理解和使用方面取得了进步,”盖格说。“我们还有很多工作要做,但在研究所和我们的合作伙伴的出色团队合作下,我们一定会帮助进一步推进这一进程,使其更接近商业用途。”